The hot air bonding process is a key step in the production of Hot Air Through Nonwoven materials. Here's a general overview of how the hot air bonding process works:
Material Formation:
The process begins with the formation of a nonwoven web. This web is typically composed of synthetic fibers, such as polypropylene or polyester, although other materials can be used.
Laying the Web:
The nonwoven web is laid out in a uniform manner, creating a consistent and even layer of fibers. This can be achieved through various methods, such as carding or air-laying.
Hot Air Introduction:
Once the web is formed, hot air is introduced into the process. The temperature of the hot air is carefully controlled to be sufficient to soften the fibers without causing them to melt. The exact temperature depends on the specific material being used.
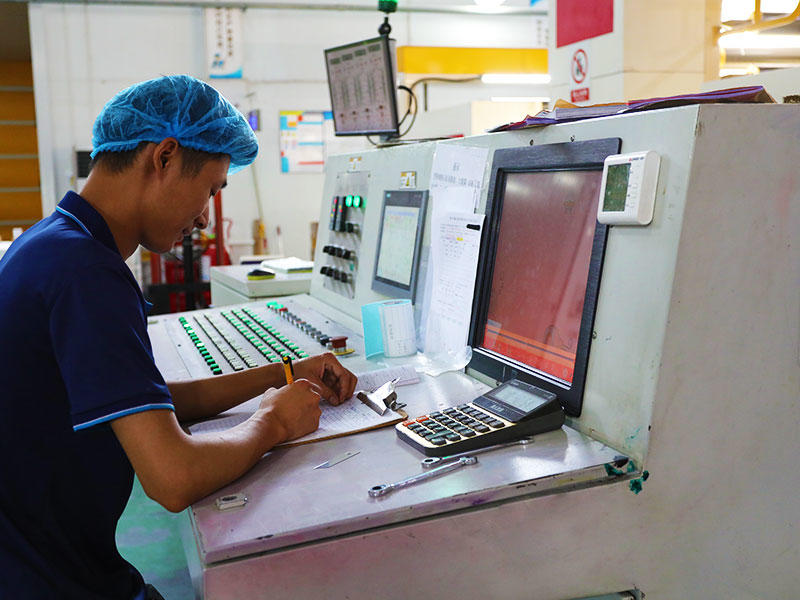
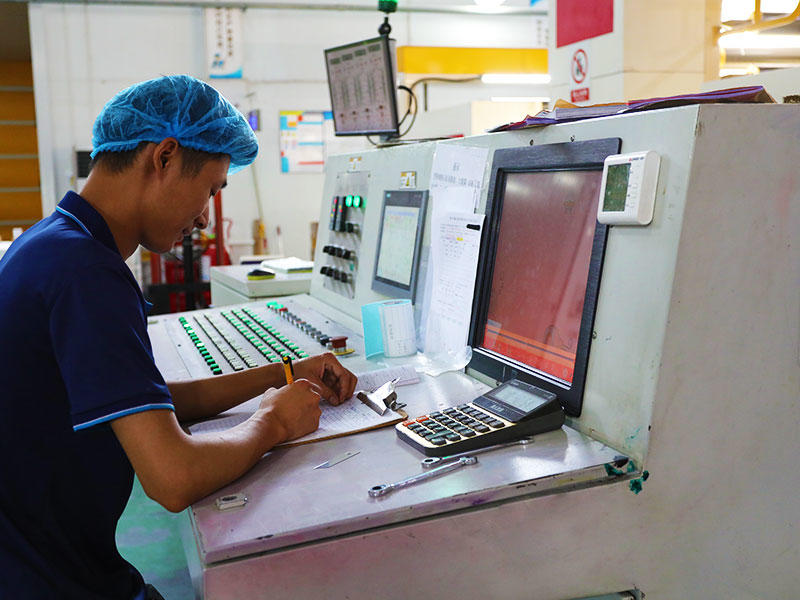
Thermal Bonding:
As the hot air circulates through the nonwoven web, it heats the fibers. The softened fibers become tacky and adhere to each other when pressed together. This is the thermal bonding stage.
Pressure Application:
Pressure is applied to the nonwoven web during or after the hot air exposure. This can be achieved using heated rollers, belts, or other compression methods. The pressure helps to create stronger bonds between the fibers.
Cooling:
After bonding, the material is allowed to cool. This cooling process helps to set the bonds and ensures the nonwoven fabric maintains its structural integrity.
Finishing Processes:
Depending on the intended application, additional finishing processes may be applied. This can include treatments for water repellency, flame resistance, or other performance enhancements.